
The conventional paper labels used for project designation on sample storage baskets was replaced by innovative Electronic Shelf Labels (ESL). This groundbreaking measure led to a significant increase in efficiency in the laboratory and a better project information overview. The project leader Bianca Wittmer, Operations Expert at TESTEX, provides insights on behalf of the entire TESTEX team into the effects and potentials of this advanced solution, which was successfully implemented across departments together with IT.
We wanted to digitise the paper-based work process to make the work as simple as possible for all departments involved, and to reduce waste. In our laboratory we have a special team that cuts and weighs samples. While these samples are being analysed in the lab, the project basket with the remaining samples is kept in temporary storage. These baskets then have to be retrieved from temporary storage for repeated sample weighing or for archiving after the tests have been completed. Before, this was done manually with a printed list of baskets, which was very time-consuming. The search alone took at least 2 hours of our time every day. Our aim was to reduce and simplify this process as much as possible to reduce waste through searching according to the Lean concept.
What were your reasons for choosing LNConsult as a solution provider?
ESL was introduced in collaboration with LNConsult as a consulting and implementation partner, who were originally recommended to us by PDi Digital. In the discussions with LNConsult, our requirements were considered, including integration with our existing Meraki access points. During the course of the implementation, it turned out that this was somewhat more complex than originally presumed due to a lack of updates from the manufacturer. The solution: additional access points were implemented by LNConsult.
Our other main requirements were:
- an API interface to our ERP system so that information can be displayed dynamically for each individual project status and workspace the project passes through
- a flexible design that allowed a lot of information to be displayed in a small space
- stackable baskets with space saving holders
- easy operation and handling of the labels

What was the intention behind the self-developed software, and how was this software linked to the ESL labels?
We needed a user friendly and quick handling of the ESL for our employees. With our app, we can make the LED lights flash in different colours according to project status. For example, if we want to search for projects that need to be archived, then we can make all these projects flash blue. This facilitates the search enormously. It was also crucial to develop a solution where none of the employees have to change anything in the database of the ERP system or in Sepioo.
How did the employees react to the new electronic system?
As with any change, there were fears among the staff, which soon disappeared after initial scepticism. We actively responded to these concerns and most of our staff were very open to the change. Since the added value for users was visible relatively quickly after the implementation, even the last silent opponent could be convinced, and everyone is now very happy with the new system.
To what extent could LNConsult assist in the development and implementation process?
LNConsult offered us the possibility to conduct a pilot project with 2 borrowed access points and 30 labels to gain initial experience and to develop our individual software solution. We were able to test several designs for the special label holder, and in addition, LNConsult provided us with technical support for the Sepioo software during the implementation phase.
What concrete results were achieved with LNConsult's solution?
We were able to achieve our desired search time not only in our originally targeted process steps, but also in additional ones. Furthermore, we now have a better overview of the number of baskets and where they are located. Even when only searching for one specific basket, it can now be found faster and more easily which saves us a lot of time and resources. In addition, our express projects are visible at first glance thanks to the option of a red background colour.
Were the project goals achieved or even exceeded?
All goals were achieved, and some were even exceeded. The implementation of the project has opened further possibilities for other optimisations, so this project was only the starting point for potential further improvement measures.
What successes were achieved?
The productivity and satisfaction of our staff has increased, and our processes have been significantly improved. By reducing search times, free capacities could be used for other tasks. As a result, we have managed to keep the targeted turnaround time for projects constant at 1 to 2 days. Another advantage is that the current project status and the dynamic data adapted to each process are very valuable for all departments.
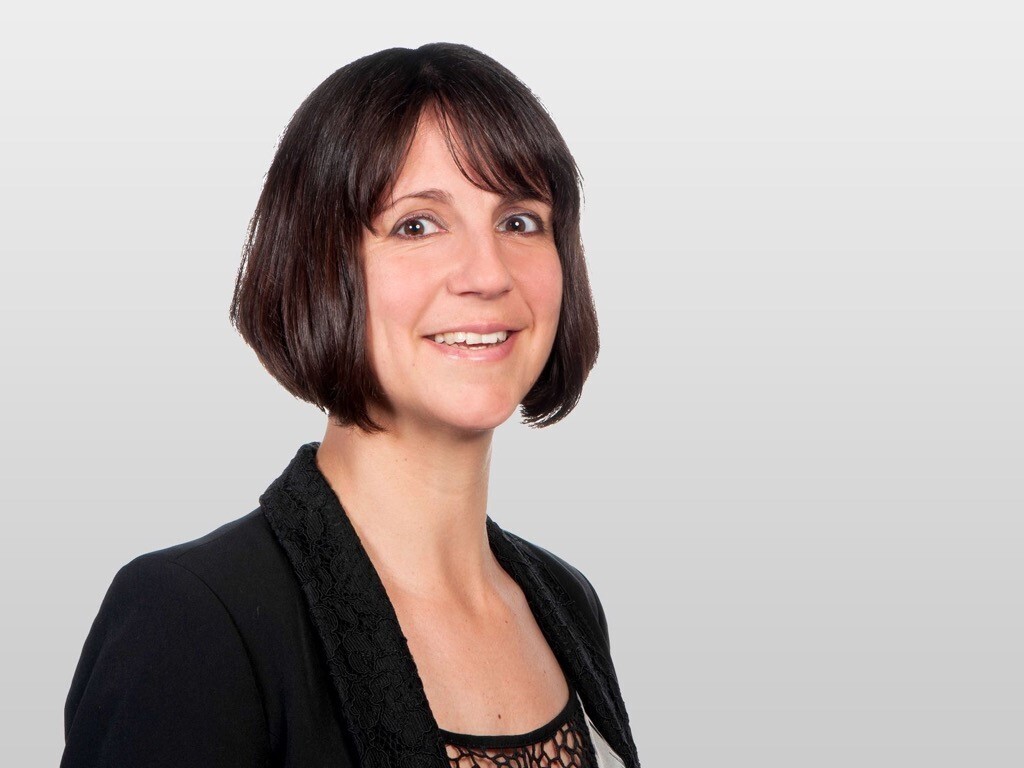
Statement from Mario Frei, one of TESTEX’s employees in sample preparation and user of the new system:
From the end user's point of view, the changeover from paper to ESL went very smoothly and without much effort. It did not affect our workflow in any way but brought numerous advantages.Before, we had to search through hundreds of paper labels to find projects we needed, but now we can light up all the labels we need with one click in our app and find them within a few minutes. Searching for the projects to be archived used to take up to an hour, if not more. Today, this task is done in just 10 minutes. The applications and interfaces for using the labels are simple and stable, so staff are able to use the tools provided with almost no training.
Since the implementation, we have also been able to make other quality improvements thanks to our software manager. One of the disadvantages of ESL is the waiting time between updates. In most cases this is not noticeable but can lead to repetition for certain tasks. The linking of baskets and projects runs almost seamlessly, but with many projects the waiting times can accumulate. In addition, we cannot pack the baskets with the ESL labels quite as tightly because they have a greater minimum height. However, this disadvantage is offset by the fact that we can archive the projects more quickly.
The advantages clearly outweigh the disadvantages and so far, the staff are very happy with the new system and have welcomed the simplified work steps.